Our Solutions
They are based on our unique expertise, derived from many years of practical experience in the field, combined with solid technical and managerial knowledge.
Product and Process Engineering
We are involved in all aspects of the development of new products and the improvement of existing products, from their initial conception through to market launch.
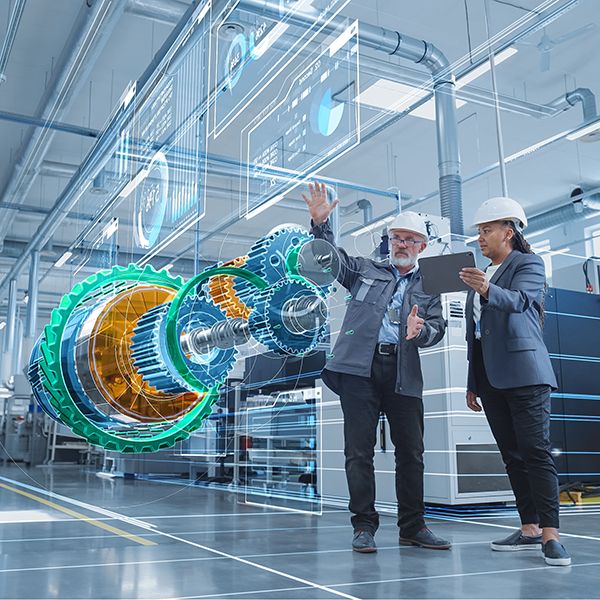
We meet our customers’ needs while taking into account technical, economic and regulatory constraints.
Our solutions are based on
- Product design
- Modelling and simulation
- Feasibility study and analysis
- Prototyping
- Manufacturing
- Validation tests
- Optimisation
We offer turnkey solutions for designing and optimising your industrial organisation.
Our aim is to guarantee maximum efficiency, optimum quality, safety and profitability in the performance of operations.
- Our expertise lies in methods and industrialisation.
- Our specialist consultants will support you in the following activities:
- Analysis of product specifications and production requirements.
- Design of the plant layout, including the location of machines, material flows and workstations.
Selection and procurement of appropriate production equipment. - Setting up manufacturing processes, including drawing up manufacturing plans, defining operating procedures and creating technical data sheets.
- Development of quality control plans and quality assurance procedures.
- Training of operators and production staff.
- Management of series production start-up.
- Development of work standards and procedures to ensure repeatability and consistency of operations.
- Introducing new technologies, automation and IT systems to improve processes.
- Supervision of construction sites
- Testing and commissioning
- Management of industrial investment projects
We support our customers at every stage of their industrial transfer projects, including
- Needs and opportunities assessment
- Strategic planning
- Analysis of existing processes
- Design of the new facility
- Logistics and supply chain planning
- Equipment and technology transfer
- Testing and validation
- Production start-up
- Monitoring and optimisation
CNC Programming & Optimisation
Whether it’s Fanuc, Siemens or ISO, you’ll benefit from an innovative, customised approach to maximising the efficiency of your CNC operations.
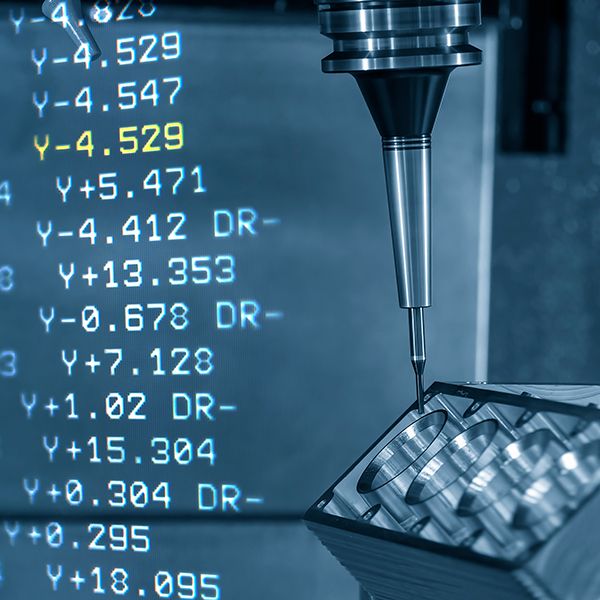
Whether you need to carry out complex turning operations or precision milling, our team of experts is ready to meet any challenge. With our extensive know-how and experience, we are able to develop bespoke CNC programmes that take full advantage of your machines’ capabilities. Our focus is on the quality and efficiency of our CNC programmes. Thanks to our expertise and use of the latest technologies, we can maximise the performance of your machines, reduce cycle times and minimise errors. Our aim is to help you optimise your manufacturing process and achieve outstanding results.
Simultaneous 5-axis machining is an essential approach for users wishing to maximise productivity and precision in machining operations. By combining the rotation of the tool and the simultaneous movement of the part on five different axes, this method enables complex shapes to be machined in a single operation and a single CNC program. The benefits are many: a significant reduction in processing time and cycle times, better tool utilisation and increased part precision. In addition, 5-axis machining offers greater design flexibility, allowing users to explore more complex shapes and contours. While this may require some upskilling to adapt to programming techniques and CAD/CAM models, the benefits in terms of output, quality and efficiency are well worth the effort. By opting for 5-axis machining, you can ensure that you exploit the full potential of your machining operations and remain competitive in the marketplace.
Parametric programming allows you to take full control of your manufacturing processes. By using modifiable variables in the code, you can easily adjust and customise your CNC programs to meet your specific needs. Whether it’s variable dimensions, process iterations or complex calculations, our team of parameterised programming experts are on hand to provide you with tailor-made solutions. With our service, you benefit from increased flexibility in production, which translates into reduced costs and lead times. You can easily change the parameters of your CNC programs without having to rewrite the entire code, allowing you to maximise productivity and adapt quickly to changing market requirements.
To optimise machine cycle time, it is essential to maximise simultaneous operations. This requires intelligent organisation of the operation plan to make efficient use of all the channels available on the machine. Other factors also come into play, such as the use of appropriate tools, the optimum configuration of machining conditions, the call-up of tools in masked time, the approach and clearance of tools, simultaneous machining and the avoidance of returns to the reference position. By taking all these aspects into account, it is possible to achieve optimum cycle times, enabling increased productivity and optimal performance in machining operations.
We carry out in-depth research to find more economical tools, and test them on your machines to optimise their service life and efficiency. Our aim is to reduce costs by offering more affordable tooling solutions, while ensuring optimum performance. We are committed to providing you with cost-effective and sustainable tooling solutions, while helping you achieve greater efficiency and productivity in your manufacturing processes.
Automated systems
When optimised, automated system offers many benefits to businesses, including a reduction in human error, increased precision and speed of operations, and better use of available resources. This translates into increased overall productivity and optimised costs.
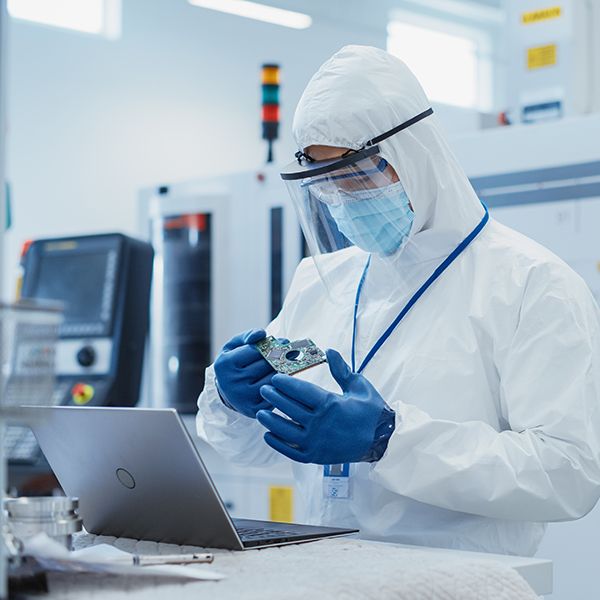
Our expertise in automation for manufacturing lines and cells offers your company undeniable advantages. Firstly, automation guarantees consistent quality, reducing human error and increasing the reliability of every product. What’s more, thanks to the flexibility and scalability of our solutions, you can easily adapt to varying production volumes and respond quickly to changing market requirements.
Our programs turn your operational needs into precise, reliable automated solutions. Our mastery of the most common languages and protocols ensures the interoperability and performance of your systems. Each program is carefully designed to guarantee optimum responsiveness, simplified maintenance and adaptability to future developments. By relying on our expertise, you benefit from tailor-made programming that integrates perfectly with your processes, maximizes performance and ensures safe operations.
We identify system vulnerabilities, implement rigorous security protocols and train staff in best practices. We can also carry out security audits, preventing risks before they occur.
The benefits to your business are manifold: reduced downtime, continuous improvement in operational efficiency, guaranteed compliance with standards and regulations, and above all, peace of mind in knowing that your automated systems are running optimally and safely.
We deploy advanced methodologies to accurately assess the current performance of your facilities. After a rigorous analysis, we identify areas of inefficiency, bottlenecks or any other opportunities for improvement.
But diagnosis is only the first step. Armed with this understanding, we propose and implement concrete improvements, be they technical optimizations, software upgrades or complete overhauls. Our aim is twofold: to increase the productivity of your systems while ensuring their long-term viability.
Comprehensive documentation and high-quality training are of paramount importance to us.
Our documentation is rigorous, up-to-date and designed to be accessible. It provides your team with all the information they need to understand, manage and optimize your automated systems. Every detail and specification is meticulously recorded to guarantee transparency and traceability.
Training is at the heart of our approach. We offer sessions tailored to all levels, from novice to expert, to ensure that every member of your team can exploit the full potential of the systems in place. Our trainers, experts in their field, use innovative teaching methods to ensure a rapid and lasting increase in skills.
Continus Improvement
We support you in the continuous improvement of your systems. Using a holistic approach, we implement best industrial practices, with the emphasis on action on the ground. We look for immediate results, but also long-term transformations, which are particularly sought after by manufacturers. We give priority to support and the sustainable transmission of our knowledge.
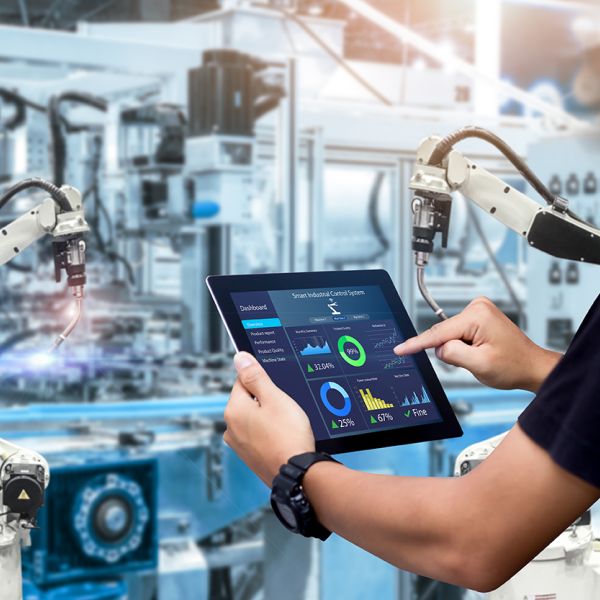
We pay particular attention to the seven types of waste: overproduction, waiting, transport, movement, excessive stocks, overprocessing and defects. These are all sources of unnecessary costs and inefficiencies in production processes.
Once waste has been identified, we work closely with our customers to implement targeted improvement programmes. These projects aim to eliminate sources of waste by optimising workflows, reducing waiting times, simplifying movements, reducing unnecessary stocks and improving quality.
We also instil a culture of continuous improvement within the companies we work with. We help put in place monitoring and control methods to measure progress and sustain the gains made.
We start by assessing the performance of the existing value chain, identifying inefficient processes, delays, excessive or insufficient stocks, communication problems and any other sources of waste or dysfunction.
Then, using our expertise, we propose customised solutions to significantly improve the value chain. This may include introducing new technologies, automating certain tasks, improving workflows, consolidating suppliers, reducing delivery times or improving product visibility and traceability throughout the chain.
We ensure that each stage of the process is properly integrated, that employees are trained to use the new systems and that key performance indicators are put in place to measure progress.
We use a variety of techniques and approaches to help our clients maximise the efficiency of their workforce, by optimising the use of working time, providing performance-based training and implementing strategic workforce planning.
We start by carrying out a detailed analysis of working time within the process under study. This enables us to identify bottlenecks, unproductive activities and inefficiencies in resource allocation. We use tools such as time analysis, workflows and key performance indicators to assess current workforce performance.
This enables us to calculate the real workforce requirement, Work-Contain / Takt-Time and allocate resources as accurately as possible.
As well as improving existing processes, we can also help you design new facilities or production lines using lean manufacturing principles.
We maximise added value while minimising waste and inefficiencies. We incorporate these principles right from the earliest stages of the design process, so that your plant or production line is optimised right from the start.
We also pay particular attention to ergonomics and safety. We take into account the physical needs of operators and reduce the risk of injury. Employee safety is an absolute priority when designing facilities or production lines.
By using the tools we have seen upstream and understanding your specific needs, objectives and constraints, we ensure that, right from the design stage, your process will meet the highest standards.
Lean manufacturing is not a single solution, but rather a continuous approach to improvement. Coaching and ongoing support help you to maintain and improve the use of lean manufacturing over the long term.
We offer training and coaching programmes tailored to your specific needs. We also address the cultural and organisational aspects of lean, emphasising the importance of management commitment, cross-functional collaboration and a culture of continuous improvement. We understand that implementing lean manufacturing can be challenging and requires regular support to overcome obstacles and maintain the momentum of continuous improvement.
Our aim is to embed lean manufacturing into the corporate culture and achieve sustainable improvements in efficiency and overall performance.
Maintenance
We optimise productivity and ensure maximum longevity of your equipment with our comprehensive range of maintenance services. Through a range of services, our team ensures that there is never any downtime in your production. We choose quality, reliability and expertise for the maintenance of your production equipment.
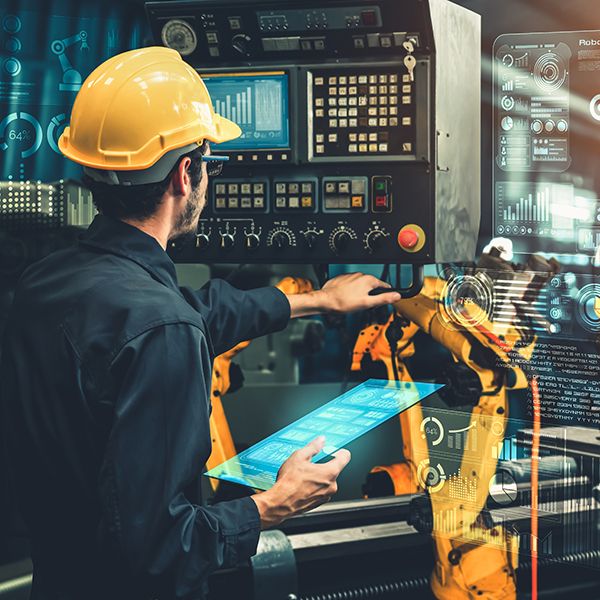
Maintenance Level I : We offer specialised training in the use, maintenance and repair of equipment. These courses are designed to enhance the technical skills of users, enabling them to deal effectively with minor problems and reduce downtime and maintenance costs.
Our training courses are tailored to specific equipment. During these courses, we provide practical knowledge of equipment operation, operating procedures, good preventive maintenance practices and early detection of potential problems. We also focus on employee safety when using and maintaining equipment, emphasising the importance of accident prevention measures, reducing reliance on external maintenance services, resulting in less unplanned downtime and lower maintenance costs. In addition, users feel more autonomous and confident in their ability to maintain and repair equipment, which contributes to greater operational efficiency.
We offer a comprehensive preventive, systematic and predictive maintenance service for production equipment. This service aims to extend equipment life, prevent costly failures and maintain high performance for our customers.
We offer systematic maintenance, which includes documented procedures for maintaining equipment. This includes activities such as visual inspection, cleaning, lubrication and replacement of worn or defective parts. These procedures detail the specific steps to be followed in carrying out maintenance tasks, ensuring a consistent and rigorous approach.
We are developing a predictive maintenance system that enables us to plan maintenance interventions proactively, taking into account information on the actual condition of the equipment. This enables us to schedule maintenance at a time that minimises interruptions to production and the associated costs. What’s more, by anticipating potential failures, we can order the necessary spare parts in advance and avoid delays in repairs.
An exhaustive diagnosis of the equipment will enable us to determine the best combined approach, thereby optimising operational costs.
We offer comprehensive calibration services to ensure the accuracy and reliability of the equipment and instruments used by our customers, such as scales, thermometers, pressure gauges, meters, electrical measuring equipment, dimensional control instruments, chemical analysers, etc.
Our calibration services are carried out by a team of qualified and experienced technicians, who follow strict procedures and use state-of-the-art equipment. We ensure that each piece of equipment is calibrated to international reference standards or to the specific specifications required by our customers.
Regular calibration of equipment is essential to maintain accuracy over time. We recommend calibration intervals appropriate to each type of equipment, depending on its frequency of use, environment and specific regulatory requirements.
We also provide calibration certificates that document the results of each calibration performed. These certificates serve as proof of equipment accuracy and compliance with applicable standards.
Our calibration services are flexible and can be tailored to the specific needs of each company. We offer long-term calibration contracts, which guarantee regular monitoring of equipment calibration. We also maintain a calibration history for each piece of equipment, making it easier to manage maintenance.
We understand the importance of electronic boards in the smooth running of equipment. As electronics experts, we can diagnose and repair faulty boards quickly, or replace them if necessary.
Our specialist technicians use state-of-the-art tools and equipment to identify problems and carry out accurate, reliable repairs. When an electronic board is faulty, our team carries out a thorough diagnosis to identify the cause of the malfunction. We use advanced test equipment to detect faults and defective components. Once the problem has been identified, we propose the appropriate solutions, whether it’s a repair to the existing board or a complete replacement.
In some cases, it may be more efficient and cost-effective to completely replace the faulty electronic board. In such cases, we make sure that we find a replacement board that is compatible with the specific equipment. We draw on our extensive network of suppliers and partners to obtain high-quality electronic boards that meet the required standards.
As well as replacing electronic boards, we also offer specific equipment replacement services. Sometimes it may be more cost-effective and practical to replace the whole equipment rather than trying to repair individual parts. In such cases, we help our customers to select and install new equipment tailored to their specific needs.
Our aim is to minimise downtime and quickly restore faulty equipment, ensuring our customers’ business continuity.
The installation of remote maintenance solution systems involves several key elements. Firstly, we program PLCs (Programmable Logic Controllers), which are electronic devices used to control and automate industrial equipment. We program PLCs according to the specifications and requirements of each company, ensuring precise and efficient control of equipment.
Secondly, we design and implement SCADA (Supervisory Control and Data Acquisition) systems to enable centralised monitoring and control of equipment and processes. SCADA systems collect data from equipment and display it in real time on a user-friendly interface. This enables operators to monitor the status of equipment, detect anomalies and take corrective action quickly.
We are also harnessing the benefits of the Internet of Things (IoT) to create extensive connectivity and real-time analysis capability. By integrating sensors and IoT devices with your equipment, we can collect continuous data on its performance, condition and usage. This data can be analysed to provide valuable insights into equipment efficiency, reliability and predictive maintenance.
Our experts work closely with customers to understand their specific needs and design bespoke remote maintenance solutions. We ensure that systems are seamlessly integrated with existing equipment, management software and corporate information systems.
We understand that equipment failures can occur at any time and can result in costly downtime for our customers. That’s why we offer 24/7 technical support specific to production resources to help them resolve problems quickly and minimise downtime.
When a problem arises, our technical support team carries out an in-depth analysis to identify the root cause. Thanks to their expertise and experience, they are able to diagnose problems quickly and propose effective solutions. In some cases, the problem can be solved remotely by guiding operators through the troubleshooting steps. In other cases, on-site intervention may be required, and our team will quickly get to the site to resolve the problem.
Our main objective is to minimise downtime and quickly restore production for our customers. We understand the importance of business continuity and do our utmost to resolve problems effectively and efficiently.
Management
Our team is with you every step of the way, providing training and technical support to ensure a smooth transition to using our solutions.
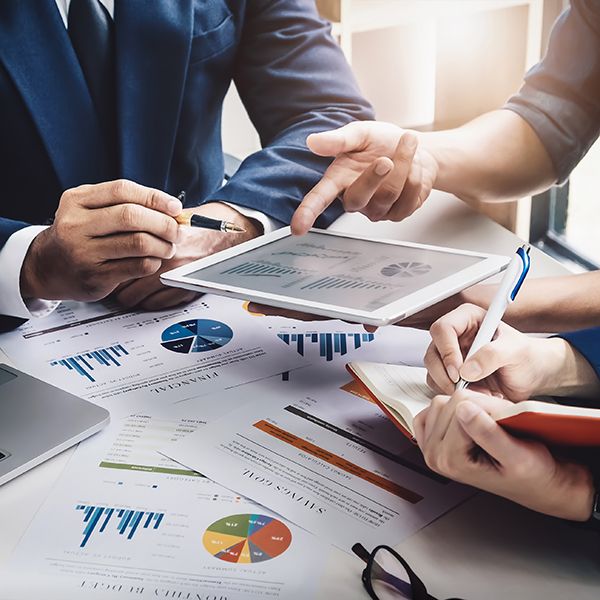
We offer project management services to ensure that each project is delivered on time, on budget and to the required specification. We work closely with our customers to plan, execute and monitor each stage of the project.
We can train companies to implement Lean Manufacturing principles, which focus on reducing waste and improving efficiency. This includes techniques such as 5S, SMED (Single-Minute Exchange of Die) and TPM (Total Productive Maintenance).