Nos Solutions
Elles s’appuient sur notre expertise unique, issue de nombreuses années de pratique sur le terrain couplée à de solides connaissances techniques et managériales.
Ingénierie Produit – Process
Nous intervenons sur touts les activités de développement de nouveaux produits et l’amélioration de produits existants, depuis leur conception initiale jusqu’à leur mise sur le marché.
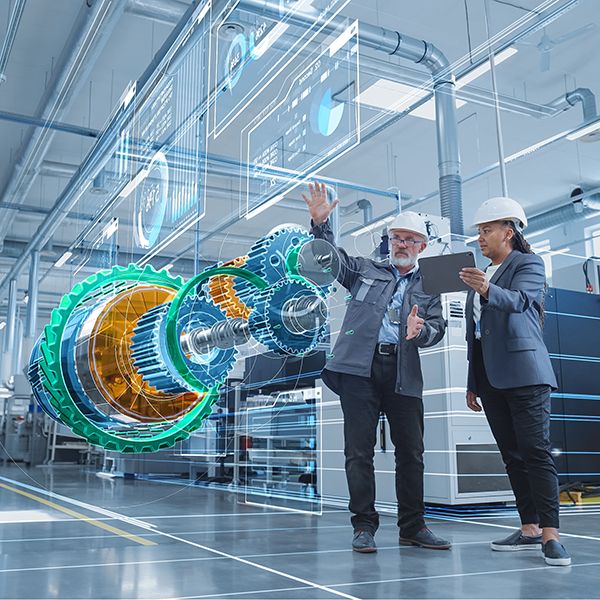
Nous répondons aux besoins de nos clients tout en prenant en compte les contraintes techniques, économiques et réglementaires.
Nos solutions s’articulent autour de:
- La conception produit
- La modélisation et la simulation
- L’étude et l’analyse de faisabilité
- Le prototypage
- La fabrication
- Les tests de validation
- L’optimisation
- Analyse des spécifications du produit et des exigences de production.
- Conception de l’agencement de l’usine, y compris l’emplacement des machines, des flux de matériaux et des postes de travail.
- Sélection et acquisition des équipements de production appropriés.
- Mise en place des processus de fabrication, y compris l’élaboration de plans de fabrication, la définition des procédures opérationnelles et la création de fiches techniques.
- Développement des plans de contrôle qualité et des procédures d’assurance qualité.
- Formation des opérateurs et du personnel de production.
- Gestion du démarrage de la production en série.
- Développement de standards de travail et de procédures pour garantir la répétabilité et la cohérence des opérations.
- Introduction de nouvelles technologies, d’automatisation et de systèmes informatiques pour améliorer les processus.
- Supervision de chantiers de réalisation
- Essais et Mise en service
- Management de projets d’investissement industriel
Nous accompagnons nos clients dans toutes les étapes de leurs projets de transfert industriel, à savoir:
- Évaluation des besoins et des opportunités
- Planification stratégique
- Analyse des processus existants
- Conception de la nouvelle installation
- Planification de la logistique et de la chaîne d’approvisionnement
- Transfert des équipements et de la technologie
- Tests et validation
- Démarrage de la production
- Suivi et optimisation
CNC Programming & Optimisation
Que se soit en Fanuc, Siemens ou ISO vous bénéficierez d’une approche innovante et personnalisée pour maximiser l’efficacité de vos opérations CNC.
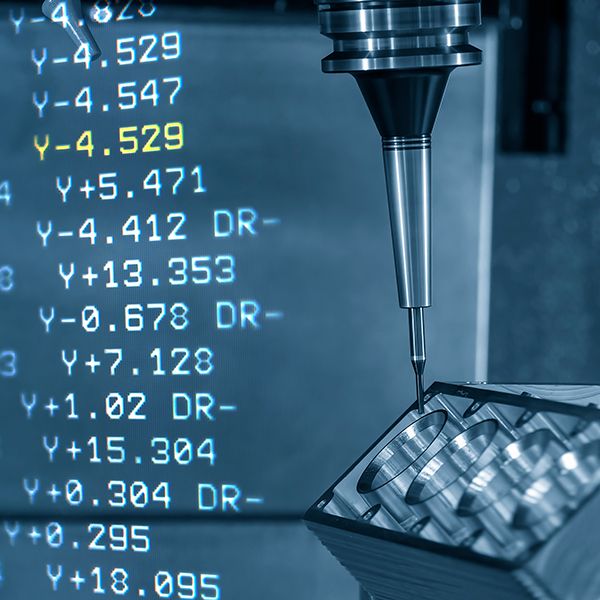
Que vous ayez besoin de réaliser des opérations de tournage complexes ou des usinages de précision en fraisage, notre équipe d’experts est prête à relever tous les défis. Avec notre savoir-faire et notre expérience approfondie, nous sommes en mesure de développer des programmes CNC sur mesure qui tirent pleinement parti des capacités de vos machines. Nous mettons l’accent sur la qualité et l’efficacité de nos programmes CNC. Grâce à notre expertise et à l’utilisation des dernières technologies, nous sommes en mesure de maximiser la performance de vos machines, réduire les temps de cycle et minimiser les erreurs. Notre objectif est de vous aider à optimiser votre processus de fabrication et à obtenir des résultats exceptionnels.
L’usinage 5 axes simultanés est une approche essentielle pour les utilisateurs qui souhaitent maximiser leur productivité et leur précision dans les opérations d’usinage. En combinant la rotation de l’outil et le mouvement simultané de la pièce sur cinq axes différents, cette méthode permet d’usiner des formes complexes en une seule opération et un seul programme CNC. Les avantages sont multiples : une réduction significative du temps de traitement et des temps de cycle, une meilleure utilisation des outils et une précision accrue des pièces. De plus, l’usinage 5 axes offre une flexibilité accrue en termes de conception, permettant aux utilisateurs d’explorer des formes et des contours plus complexes. Bien que cela puisse nécessiter une montée en compétences pour s’adapter aux techniques de programmation et aux modèles en CAO/FAO, les avantages en termes de rendement, de qualité et d’efficacité en valent largement la peine. En optant pour l’usinage 5 axes, vous vous assurez d’exploiter pleinement le potentiel de vos opérations d’usinage et de rester compétitif sur le marché.
La programmation paramétrée vous permet de prendre le contrôle total de vos processus de fabrication. En utilisant des variables modifiables dans le code, vous pouvez facilement ajuster et personnaliser vos programmes CNC en fonction de vos besoins spécifiques. Que ce soit pour des dimensions variables, des itérations de processus ou des calculs complexes, notre équipe d’experts en programmation paramétrée est là pour vous fournir des solutions sur mesure. Avec notre service, vous bénéficiez d’une flexibilité accrue dans la production, ce qui se traduit par une réduction des coûts et des délais. Vous pouvez facilement modifier les paramètres de vos programmes CNC sans avoir à réécrire l’intégralité du code, ce qui vous permet d’optimiser votre productivité et de vous adapter rapidement aux exigences changeantes du marché.
Pour optimiser le temps de cycle, il est essentiel de maximiser les opérations simultanées. Cela nécessite une organisation intelligente du plan d’opération afin d’utiliser efficacement tous les canaux disponibles sur la machine. D’autres facteurs entrent également en jeu, tels que l’utilisation d’outils appropriés, la configuration optimale des conditions d’usinage, l’appel d’outils en temps masqué, l’approche et le dégagement des outils, les usinages simultanés et l’évitement des retours en position de référence. En prenant en compte tous ces aspects, il est possible d’atteindre un temps de cycle optimal, permettant une productivité accrue et des performances optimales dans les opérations d’usinage.
Nous effectuons des recherches approfondies pour trouver des outils plus économiques et nous réalisons des essais sur vos machines afin d’optimiser leur durée de vie et leur efficacité. Notre objectif est de réduire les coûts en proposant des solutions d’outillage plus abordables, tout en garantissant des performances optimales. Nous sommes déterminés à vous offrir des solutions d’outillage rentables et durables, tout en vous aidant à atteindre une efficacité et une productivité supérieures dans vos processus de fabrication.
Automatisme
L’automatisme, lorsque il est optimisé, offre de nombreux avantages aux entreprises, notamment une réduction des erreurs humaines, une augmentation de la précision et de la rapidité des opérations, ainsi qu’une meilleure utilisation des ressources disponibles. Cela se traduit par une augmentation de la productivité globale et une optimisation des coûts.
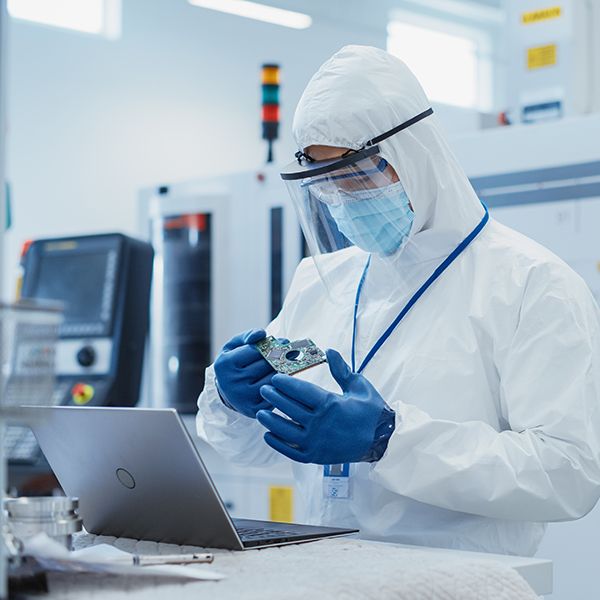
Notre expertise en matière d’automatismes pour lignes et cellules de fabrication offre à votre entreprise des avantages incontestables. Tout d’abord, l’automatisation garantit une constance de qualité, réduisant les erreurs humaines et augmentant la fiabilité de chaque produit. De plus, grâce à la flexibilité et l’évolutivité de nos solutions, vous pouvez facilement vous adapter à des volumes de production variables et répondre rapidement aux exigences changeantes du marché.
Nos programmes permettent de transformer vos besoins opérationnels en solutions automatisées précises et fiables. Grâce à une maîtrise des langages et protocoles les plus courants, nous assurons l’interopérabilité et la performance de vos systèmes. Chaque programme est soigneusement élaboré pour garantir une réactivité optimale, une maintenance simplifiée et une adaptabilité aux évolutions futures. En faisant confiance à notre expertise, vous bénéficiez d’une programmation sur mesure, qui s’intègre parfaitement à vos processus, maximise le rendement et assure la sécurité des opérations.
Nous identifions les points vulnérables des systèmes, instaurons des protocoles de sécurité rigoureux et formons le personnel aux bonnes pratiques. Nous pouvons aussi effectuer des audits de sécurité, prévenant les risques avant qu’ils ne surviennent.
Les avantages au sein de votre entreprise sont multiples : réduction des temps d’arrêt, amélioration constante de l’efficacité opérationnelle, garantie d’une conformité aux normes et régulations, et surtout, une tranquillité d’esprit en sachant que vos systèmes automatisés fonctionnent de manière optimale et sûre.
Nous déployons des méthodologies avancées pour évaluer avec précision la performance actuelle de vos installations. Après une analyse rigoureuse, nous identifions les domaines d’inefficacité, les goulots d’étranglement ou toute autre opportunité d’amélioration.
Mais le diagnostic n’est que la première étape. Forts de cette compréhension, nous proposons et mettons en œuvre des améliorations concrètes, qu’il s’agisse d’optimisations techniques, de mises à jour logicielles ou de refontes complètes. Notre objectif est double : augmenter la productivité de vos systèmes tout en assurant leur pérennité.
Nous accordons une importance primordiale à la documentation complète et à la formation de haute qualité.
Notre documentation est rigoureuse, à jour et conçue pour être accessible. Elle fournit à votre équipe toutes les informations nécessaires pour comprendre, gérer et optimiser vos systèmes automatisés. Chaque détail, chaque spécification est méticuleusement enregistré pour garantir la transparence et la traçabilité.
La formation, quant à elle, est au cœur de notre démarche. Nous proposons des sessions adaptées à tous les niveaux, des novices aux experts, pour assurer que chaque membre de votre équipe puisse exploiter pleinement le potentiel des systèmes en place. Nos formateurs, experts dans leur domaine, utilisent des méthodes pédagogiques innovantes pour assurer une montée en compétence rapide et durable.
Amélioration Continue
Nous vous accompagnons dans l’amélioration continue de vos systèmes. Grâce à une approche holistique, nous mettons en œuvre les bonnes pratiques industrielles, en mettant l’accent sur l’action sur le terrain. Nous cherchons des résultats immédiats mais aussi les transformations à long terme, qui sont particulièrement recherchées par les industriels. Nous privilégions l’accompagnement et la transmission durable de nos connaissances.
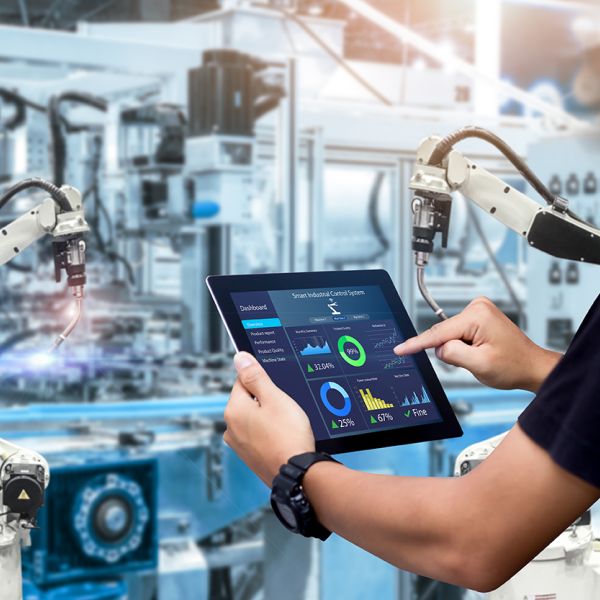
Nous sommes particulièrement attentifs aux sept types de gaspillages : à savoir la surproduction, l’attente, le transport, le mouvement, les stocks excessifs, le surprocessing et les défauts. Ils sont autant de sources de coûts inutiles et d’inefficacités dans les processus de production.
Une fois les gaspillages identifiés, nous travaillons en étroite collaboration avec nos clients pour mettre en place des chantiers d’amélioration ciblés. Ces chantiers visent à éliminer les sources de gaspillage en optimisant les flux de travail, en réduisant les temps d’attente, en simplifiant les mouvements, en réduisant les stocks inutiles et en améliorant la qualité.
Nous insufflons également la culture de l’amélioration continue au sein des entreprises avec lesquelles nous travaillons. Nous aidons à mettre en place des méthodes de suivi et de contrôle pour mesurer les progrès réalisés et pour maintenir les gains obtenus.
Nous commençons par évaluer la performance de la chaîne de valeur existante, en identifiant les processus inefficaces, les retards, les stocks excessifs ou insuffisants, les problèmes de communication et toute autre source de gaspillage ou de dysfonctionnement.
Ensuite, grâce à notre expertise, nous proposons des solutions personnalisées pour améliorer significativement la chaîne de valeur. Cela peut inclure l’introduction de nouvelles technologies, l’automatisation de certaines tâches, l’amélioration des flux, la consolidation des fournisseurs, la réduction des délais de livraison ou encore l’amélioration de la visibilité et de la traçabilité des produits tout au long de la chaîne.
Nous nous assurons que chaque étape du processus est correctement intégrée, que les employés sont formés pour utiliser les nouveaux systèmes et que les indicateurs clés de performance sont mis en place pour mesurer les progrès réalisés.
Nous utilisons différentes techniques et approches pour aider nos clients à maximiser l’efficacité de leur main d’œuvre, en optimisant l’utilisation du temps de travail, en fournissant une formation axée sur la performance et en mettant en place une planification stratégique de la main-d’œuvre.
Nous commençons par réaliser une analyse détaillée du temps de travail au sein du process étudié. Cela nous permet d’identifier les goulots d’étranglement, les activités non productives et les inefficacités dans l’allocation des ressources. Nous utilisons des outils tels que les chrono analyses, les flux de travail et les indicateurs clés de performance pour évaluer la performance actuelle de la main d’œuvre.
Cela nous permet de calculer le besoin réel en main d’oeuvre, Work-Contain / Takt-Time et d’affecter au plus juste les ressources.
En plus de l’amélioration des processus existants, nous vous aidons également à concevoir de nouvelles installations ou lignes de production en utilisant les principes du lean manufacturing.
Nous maximisons la valeur ajoutée tout en minimisant les gaspillages et les inefficacités. Nous intégrons ces principes dès les premières étapes de la conception, ce qui permet d’obtenir des installations ou des lignes de production optimisées dès le départ.
De plus, nous accordons une attention particulière à l’ergonomie et à la sécurité. Nous prenons en compte les besoins physiques des opérateurs et réduisons les risques de blessures. La sécurité des employés est une priorité absolue lors de la conception des installations ou des lignes de production.
En utilisant les outils vus en amont et en comprenant vos besoins spécifiques, vos objectifs et vos contraintes, nous nous assurons que, dès la conception, votre process atteindra des sommets d’exigence.
Le lean manufacturing n’est pas une solution unique, mais plutôt une approche continue de l’amélioration. Le coaching et le support continu vous aident à maintenir et à améliorer l’utilisation du lean manufacturing sur le long terme.
Nous proposons des programmes de formation et coaching adaptés aux besoins spécifiques de chacun. Nous abordons également les aspects culturels et organisationnels du lean, en insistant sur l’importance de l’engagement de la direction, de la collaboration interfonctionnelle et de la culture d’amélioration continue. Nous comprenons que la mise en œuvre du lean manufacturing peut être un défi et nécessite un accompagnement régulier pour surmonter les obstacles et maintenir l’élan de l’amélioration continue.
Notre objectif est d’ intégrer le lean manufacturing dans la culture d’entreprise et de réaliser des améliorations durables dans leur efficacité et leur performance globale.
Maintenance
Nous optimisons la productivité et assurons une longévité maximale de vos équipements avec notre gamme complète de services de maintenance. A travers différents services notre équipe s’assure qu’il n’y a jamais de temps d’arrêt dans votre production. Nous faisons le choix de la qualité, de la fiabilité et de l’expertise pour la maintenance de vos équipements de production.
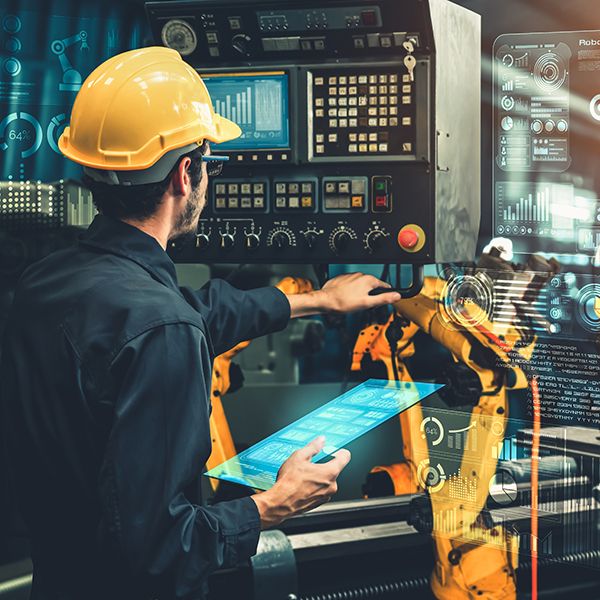
Maintenance Niveau I : Nous proposons des formations spécialisées sur l’utilisation, la maintenance et la réparation des équipements. Ces formations visent à renforcer les compétences techniques des utilisateurs, leur permettant ainsi de gérer efficacement les petits problèmes et de réduire les temps d’arrêt ainsi que les coûts de maintenance.
Nos formations sont adaptées aux équipements spécifiques. Lors de ces formations, nous fournissons des connaissances pratiques sur le fonctionnement des équipements, les procédures d’utilisation, les bonnes pratiques de maintenance préventive et la détection précoce des problèmes potentiels. Nous mettons également l’accent sur la sécurité des employés lors de l’utilisation et de la maintenance des équipements, en soulignant l’importance des mesures de prévention des accidents, nous réduisons la dépendance aux services externes de maintenance, ce qui se traduit par une diminution des temps d’arrêt non planifiés et des coûts de maintenance. De plus, les utilisateurs se sentent plus autonomes et confiants dans leur capacité à maintenir et à réparer les équipements, ce qui contribue à une meilleure efficacité opérationnelle.
Nous proposons un service complet de maintenance préventive, systématique et prédictive des équipements de production. Ce service vise à prolonger la durée de vie des équipements, à prévenir les défaillances coûteuses et à maintenir un rendement élevé pour nos clients.
Nous proposons une maintenance systématique, qui comprend des procédures documentées pour la maintenance des équipements. Elle comprend des activités telles que l’inspection visuelle, le nettoyage, la lubrification et le remplacement des pièces usées ou défectueuses. Ces procédures détaillent les étapes spécifiques à suivre pour effectuer les tâches de maintenance, assurant ainsi une approche cohérente et rigoureuse.
Nous mettons au point un système de maintenance prédictive qui permet de planifier les interventions de maintenance de manière proactive, en tenant compte des informations sur l’état réel des équipements. Cela nous permet de planifier la maintenance à un moment qui minimise les interruptions de la production et les coûts associés. De plus, en anticipant les défaillances potentielles, nous pouvons commander à l’avance les pièces de rechange nécessaires et éviter les retards dans la réparation.
Un diagnostiques exhaustif de l’équipement permettra de déterminer au mieux une approche combinée, optimisant ainsi les coûts opérationnel.
Nous proposons des services de calibrage complets pour garantir la précision et la fiabilité des équipements et des instruments utilisés par nos clients, tels que les balances, les thermomètres, les manomètres, les compteurs, les appareils de mesure électrique, les instruments de contrôle dimensionnel, les analyseurs chimiques…
Nos services de calibrage sont effectués par une équipe de techniciens qualifiés et expérimentés, qui suivent des procédures strictes et utilisent des équipements de pointe. Nous nous assurons que chaque équipement est calibré conformément aux normes de références internationales ou aux spécifications spécifiques exigées par nos clients.
Le calibrage régulier des équipements est essentiel pour maintenir leur précision au fil du temps. Nous recommandons des intervalles de calibrage adaptés à chaque type d’équipement, en fonction de sa fréquence d’utilisation, de son environnement et des exigences réglementaires spécifiques.
Nous fournissons également des certificats de calibrage qui documentent les résultats de chaque calibrage effectué. Ces certificats servent de preuve de la précision des équipements et de conformité aux normes applicables.
Nos services de calibrage sont flexibles et peuvent être adaptés aux besoins spécifiques de chaque entreprise. Nous proposons des contrats de calibrage à long terme, qui garantissent un suivi régulier du calibrage des équipements. Nous tenons également à jour un historique des calibrages effectués pour chaque équipement, ce qui facilite la gestion de la maintenance.
Nous comprenons l’importance des cartes électroniques dans le bon fonctionnement des équipements. En tant qu’experts en électronique, nous sommes en mesure de diagnostiquer et de réparer rapidement les cartes défectueuses, ou de les remplacer si nécessaire.
Nos techniciens spécialisés utilisent des outils et des équipements de pointe pour identifier les problèmes et effectuer des réparations précises et fiables. Lorsqu’une carte électronique est défectueuse, notre équipe effectue un diagnostic approfondi pour identifier la cause du dysfonctionnement. Nous utilisons des équipements de tests avancés pour détecter les défauts et les composants défectueux. Une fois le problème identifié, nous proposons les solutions appropriées, qu’il s’agisse d’une réparation de la carte existante ou d’un remplacement complet.
Dans certains cas, il peut être plus efficace et économique de remplacer complètement la carte électronique défectueuse. Dans de tels cas, nous nous assurons de trouver une carte de remplacement compatible avec l’équipement spécifique. Nous nous appuyons sur notre vaste réseau de fournisseurs et de partenaires pour obtenir des cartes électroniques de haute qualité et répondant aux normes requises.
En plus du remplacement des cartes électroniques, nous offrons également des services de remplacement des équipements spécifiques. Parfois, il peut être plus rentable et pratique de remplacer l’ensemble de l’équipement plutôt que de tenter de réparer des pièces individuelles. Dans de tels cas, nous aidons nos clients à sélectionner et à installer de nouveaux équipements adaptés à leurs besoins spécifiques.
Notre objectif est de minimiser les temps d’arrêt et de restaurer rapidement les équipements en panne, garantissant ainsi la continuité des opérations de nos clients.
L’installation de systèmes de solution de télémaintenance comprend plusieurs éléments clés. Tout d’abord, nous effectuons la programmation de PLC (Programmable Logic Controller), qui est un dispositif électronique utilisé pour contrôler et automatiser les équipements industriels. Nous programmons les PLC en fonction des spécifications et des exigences de chaque entreprise, garantissant un contrôle précis et efficace des équipements.
Ensuite, nous concevons et mettons en œuvre des systèmes SCADA (Supervisory Control and Data Acquisition) pour permettre la surveillance et le contrôle centralisés des équipements et des processus. Les systèmes SCADA collectent les données provenant des équipements et les affichent en temps réel sur une interface conviviale. Cela permet aux opérateurs de surveiller l’état des équipements, de détecter les anomalies et de prendre des mesures correctives rapidement.
Nous exploitons également les avantages de l’Internet des objets (IoT) pour créer une connectivité étendue et une capacité d’analyse en temps réel. En intégrant des capteurs et des dispositifs IoT à vos équipements, nous pouvons recueillir des données en continu sur leur performance, leur état et leur utilisation. Ces données peuvent être analysées pour obtenir des informations précieuses sur l’efficacité, la fiabilité et la maintenance prédictive des équipements.
Nos experts travaillent en étroite collaboration avec les clients pour comprendre leurs besoins spécifiques et concevoir des solutions de télémaintenance sur mesure. Nous nous assurons que les systèmes sont intégrés de manière transparente avec les équipements existants, les logiciels de gestion et les systèmes d’information de l’entreprise.
Nous comprenons que les pannes d’équipement peuvent survenir à tout moment et qu’elles peuvent entraîner des temps d’arrêt coûteux pour nos clients. C’est pourquoi nous offrons un support technique 24/7 spécifique à des moyens de production pour les aider à résoudre rapidement les problèmes et à minimiser les temps d’arrêt.
Lorsqu’un problème survient, notre équipe de support technique effectue une analyse approfondie pour identifier la cause racine du problème. Grâce à leur expertise et à leur expérience, ils sont en mesure de diagnostiquer rapidement les problèmes et de proposer des solutions efficaces. Dans certains cas, le problème peut être résolu à distance en guidant les opérateurs à travers les étapes de dépannage. Dans d’autres cas, une intervention sur site peut être nécessaire, et notre équipe se rend rapidement sur place pour résoudre le problème.
Notre objectif principal est de minimiser les temps d’arrêt et de rétablir rapidement la production pour nos clients. Nous comprenons l’importance de la continuité des opérations et nous faisons tout notre possible pour résoudre les problèmes de manière efficace et efficiente.
Management
Notre équipe vous accompagne tout au long du processus, en fournissant une formation et un support technique pour assurer une transition en douceur vers l’utilisation de nos solutions.
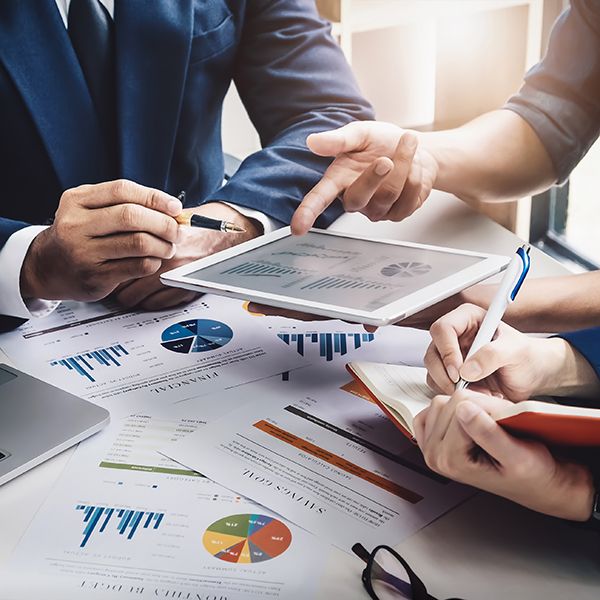
Nous offrons des services de gestion de projets pour garantir que chaque projet est livré dans les délais impartis, dans les limites budgétaires et selon les spécifications requises. Nous travaillons en étroite collaboration avec nos clients pour planifier, exécuter et surveiller chaque étape du projet.
Nous pouvons former les entreprises à la mise en œuvre des principes du Lean Manufacturing, qui se concentrent sur la réduction des déchets et l’amélioration de l’efficacité. Cela inclut des techniques telles que le 5S, le SMED (Single-Minute Exchange of Die) et le TPM (Total Productive Maintenance).